Welcome to our ultimate guide on concrete pricing per cubic meter in New Zealand! Whether you’re a homeowner planning a DIY project, a contractor managing a construction site, or simply curious about the costs involved, understanding concrete pricing is essential for budgeting and decision-making. Concrete prices in NZ can vary due to factors such as location, supplier, concrete type, and additional costs like delivery and pumping fees. With rising material costs and fluctuating demand, knowing what to expect can help you save money while ensuring you get the right mix for your project. In this guide, we’ll break down the average cost per cubic meter, key factors affecting pricing, and practical tips to help you get the best deal without compromising on quality.
The average concrete price per cubic meter in New Zealand ranges from $180 to $250, depending on factors like concrete type, supplier, delivery fees, and project location. Specialty mixes, such as reinforced or decorative concrete, can cost more. To get the best price, compare multiple suppliers, order in bulk, and consider local options to reduce transport costs.
- Understanding Concrete Pricing In NZ
- Factors Affecting The Cost Of Concrete In New Zealand
- Type Of Concrete: Regular, Reinforced, Decorative, Specialty Mixes
- Supplier & Location: Differences In Pricing Between Major Cities Vs. Rural Areas
- Delivery Costs: How Distance And Accessibility Impact Transport Fees
- Strength & Quality: How Different Concrete Strengths (MPA Ratings) Affect Pricing
- Seasonal Price Fluctuations: Demand During Peak Construction Seasons
- Additional Costs: Pumping Fees, Admixtures, Additives
- Breakdown Of Concrete Prices In NZ (2025 Estimates)
- How To Get The Best Price For Concrete In NZ
- DIY Vs. Hiring A Professional: Cost Considerations
- Common Mistakes That Can Increase Concrete Costs
- Underestimating Material Needs: Leads To Additional Small Orders At A Higher Cost
- Ignoring Site Preparation: Poor Ground Conditions May Require Extra Work
- Last-Minute Changes To Mix Or Quantity: Can Increase Costs Significantly
- Choosing The Wrong Concrete Mix For The Project: May Lead To Future Repairs
- FAQs: About Concrete Price Per Cubic Meter In NZ
- Conclusion
Understanding Concrete Pricing In NZ
When planning a construction project, whether it’s a simple backyard patio or a large-scale commercial building, understanding concrete pricing in New Zealand is crucial. Concrete is a fundamental material in construction, known for its durability, strength, and versatility. However, its cost can vary based on several factors, making it essential to grasp how pricing is calculated and what influences the final cost per cubic meter.
Why Is Concrete Measured In Cubic Meters?
Concrete is sold and priced per cubic meter (m³) because it is a fluid material before it sets. Measuring by volume ensures that buyers get the exact amount needed for their project without unnecessary waste or shortages.
One cubic meter of concrete is equivalent to a space measuring 1m x 1m x 1m, which allows suppliers and contractors to estimate the total volume required for a project accurately. Unlike other construction materials that might be priced by weight (like gravel or sand), concrete’s volume-based pricing is more practical since its density and composition can vary depending on the mix design.
What Is The Average Concrete Price Per Cubic Meter In NZ?
The cost of concrete in New Zealand typically falls within the range of $180 to $250 per cubic meter. However, this price can fluctuate depending on multiple factors, including:
- Type Of Concrete – Basic concrete mixes are more affordable, while high-strength or decorative concretes cost more.
- Supplier Location – Prices vary between urban centers (Auckland, Wellington, Christchurch) and rural areas due to transportation costs.
- Delivery Fees – The distance from the supplier to the site plays a significant role in the total cost.
- Additional Additives – Special mixes with waterproofing, color pigments, or reinforcements increase the price per cubic meter.
While these figures provide a general guideline, it’s always best to request a quote from local suppliers to get the most accurate pricing based on your project’s specific requirements.
Residential Vs. Commercial Concrete Pricing
The cost of concrete can differ significantly depending on whether it is for a residential or commercial project.
- Residential Concrete Pricing: Homeowners typically order concrete for driveways, patios, footpaths, and small home renovations. These projects usually require lower-strength concrete (such as 20MPA) and smaller volumes, which can lead to slightly higher per-unit costs due to smaller batch orders. Residential projects may also incur additional delivery fees if the quantity ordered is below the supplier’s minimum requirement.
- Commercial Concrete Pricing: Larger-scale projects, such as office buildings, bridges, and industrial foundations, often require high-strength concrete (30MPA or above) and specialized mixes. Since commercial projects involve bulk ordering, the price per cubic meter tends to be lower due to economies of scale. Additionally, large construction companies may have negotiated supplier contracts, which can further reduce costs.
Understanding these differences can help homeowners, builders, and contractors make informed decisions when budgeting for their projects.
How Bulk Orders Vs. Small Orders Affect Cost
Ordering concrete in bulk can lead to significant cost savings, while smaller orders tend to have higher per-unit costs. Here’s why:
- Bulk Orders: When purchasing large quantities of concrete (e.g., 10m³ or more), suppliers often provide discounted rates. This is because batching and delivering concrete in larger volumes is more efficient for suppliers, reducing operational costs. Bulk orders also minimize delivery expenses, as fewer trips are needed to transport the material.
- Small Orders: If you’re ordering less than 3m³, the price per cubic meter may be higher due to minimum delivery charges. Many suppliers charge extra for small loads since it is less efficient to mix and transport small amounts of concrete. Some suppliers even have a minimum order requirement, meaning that even if you only need 1m³, you might have to pay for a higher volume.
To save money, it’s advisable to:
- Combine multiple concrete projects into one order to reach bulk pricing thresholds.
- Coordinate with neighbors or nearby builders to place a joint order and split delivery costs.
- Plan ahead and calculate the exact volume needed to avoid ordering small additional batches, which can be costly.
Understanding how concrete pricing works in New Zealand helps ensure that you budget effectively and avoid unexpected costs. Whether you’re a homeowner working on a DIY project or a contractor handling a large commercial build, knowing the average cost per cubic meter, the differences between residential and commercial pricing, and how bulk ordering can save money will help you make the best purchasing decisions.
Before placing an order, always compare quotes from multiple suppliers, consider bulk discounts, and factor in additional costs such as delivery and additives. By doing so, you can get the best value for your investment while ensuring high-quality results for your project.
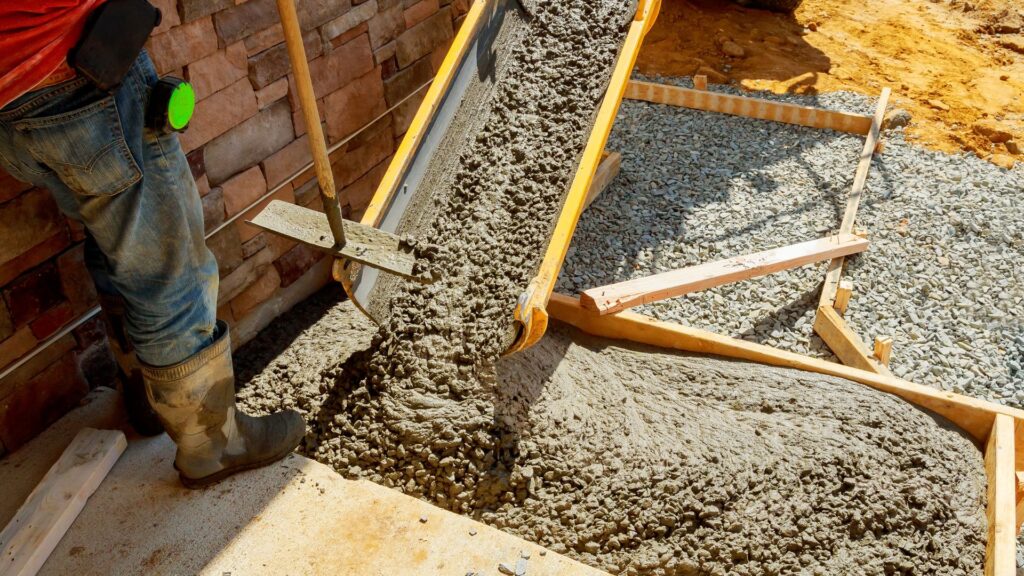
Factors Affecting The Cost Of Concrete In New Zealand
When budgeting for a concrete project in New Zealand, it’s important to understand the various elements that influence pricing. From the type of concrete you choose to where you source it, multiple factors can impact the final cost per cubic meter. Below is a detailed breakdown of the key factors that determine concrete prices in NZ.
Type Of Concrete: Regular, Reinforced, Decorative, Specialty Mixes
The type of concrete you select plays a major role in the overall cost. Regular concrete is typically the most affordable option, used for standard residential projects like driveways and footpaths. If you require reinforced concrete, which includes steel mesh or fibers for added strength, expect to pay a higher price due to the extra materials involved.
For those looking to enhance aesthetics, decorative concrete, such as exposed aggregate or colored concrete, can significantly raise costs. These variations require specialized materials and additional labor to achieve the desired finish. Lastly, specialty concrete mixes, such as high-performance or self-compacting concrete, come at a premium due to their advanced formulation and strength properties.
Supplier & Location: Differences In Pricing Between Major Cities Vs. Rural Areas
Your location in New Zealand heavily impacts the price of concrete. Suppliers in major cities like Auckland, Wellington, and Christchurch often have better infrastructure, higher competition, and larger production capacities, which can lead to slightly lower prices.
On the other hand, rural areas may experience higher costs due to limited supplier options and the additional transportation required to deliver materials. The further you are from a batching plant, the more you’ll pay for logistics, making it essential to source from the nearest available supplier when possible.
Delivery Costs: How Distance And Accessibility Impact Transport Fees
Concrete is a perishable material that needs to be delivered and poured within a limited timeframe. The further the delivery site is from the supplier’s batching plant, the higher the transport fees.
Additionally, site accessibility plays a big role in pricing. If a concrete truck has difficulty reaching your location due to narrow roads, steep terrain, or other obstacles, extra costs may be incurred. In some cases, you might need a concrete pump, which adds to the total expense. To reduce delivery costs, consider ordering from the closest supplier and ensuring that your site is easily accessible.
Strength & Quality: How Different Concrete Strengths (MPA Ratings) Affect Pricing
Concrete strength is measured in megapascals (MPA), and different projects require different strength levels. Lower-strength concrete, such as 20MPA, is commonly used for non-structural applications like footpaths and light-duty driveways. This type is more affordable compared to 30MPA or 40MPA concrete, which is designed for structural integrity, commercial applications, and heavy loads.
Higher-strength concrete requires more cement and advanced additives, which increase costs. Before purchasing, always check your project specifications to ensure you’re using the correct strength, as choosing the wrong type could lead to premature failure or unnecessary expenses.
Seasonal Price Fluctuations: Demand During Peak Construction Seasons
Concrete prices in New Zealand can fluctuate based on seasonal demand. During warmer months, particularly spring and summer, construction activity peaks, increasing the demand for concrete. Suppliers may adjust their prices due to higher production demands and potential material shortages.
Conversely, winter months typically see a slowdown in construction, leading to more competitive pricing. If your project timeline allows flexibility, consider scheduling your concrete purchase during the off-season to potentially save on costs.
Additional Costs: Pumping Fees, Admixtures, Additives
Beyond the base price of concrete, there are additional costs that may apply depending on your project’s needs. Pumping fees are one of the most common extra expenses, especially for sites where a standard concrete truck cannot directly pour the mix. Pumping ensures efficient placement but adds to the overall budget.
Other potential additives and admixtures include:
- Waterproofing Agents – Ideal for foundations and areas exposed to moisture, but come at an added cost.
- Retarders & Accelerators – Used to slow down or speed up the curing process, depending on weather conditions.
- Plasticizers & Superplasticizers – Improve workability without affecting strength, commonly used in high-performance concrete.
These enhancements can improve durability and performance, but they also increase the final price. Always discuss with your supplier whether these additional materials are necessary for your specific project.
The cost of concrete per cubic meter in New Zealand isn’t just about the base material—it’s influenced by various external factors such as type, location, transportation, strength, seasonality, and extra fees. Understanding these variables can help you make smarter purchasing decisions and avoid unexpected costs. By planning ahead, comparing suppliers, and optimizing delivery logistics, you can ensure that you get the best quality concrete at the most competitive price.

Breakdown Of Concrete Prices In NZ (2025 Estimates)
When planning any construction project, understanding the cost of concrete per cubic meter is crucial. Whether you’re pouring a new driveway, building a foundation, or tackling a DIY project, knowing how much you’ll spend can help you budget wisely and avoid unexpected expenses. Concrete prices in New Zealand vary based on several factors, including the type of mix, supplier, delivery distance, and additional additives. Below, we break down the estimated costs for different types of concrete in 2025.
Basic Concrete Mix: $180 – $250 Per Cubic Meter
For standard construction projects such as driveways, footpaths, and small foundations, a basic concrete mix is the most commonly used and affordable option. This mix typically includes cement, sand, and aggregate in standard proportions, making it suitable for general-purpose applications.
- Best For: Driveways, footpaths, patios, general residential use
- Average Price: $180 – $250 per cubic meter
- Pros: Cost-effective, widely available, easy to work with
- Cons: Not as strong or durable as reinforced or specialty concrete
If you’re working on a budget-friendly home project, this mix is ideal, but make sure to check with your local suppliers as prices may vary depending on location and bulk order discounts.
Premium-Grade Or Reinforced Concrete: $250 – $350 Per Cubic Meter
For structures that require higher strength and durability, premium-grade or reinforced concrete is a better choice. This type of concrete typically contains higher cement content and reinforcing materials such as steel mesh or fibers, increasing its load-bearing capacity.
- Best For: Structural foundations, commercial buildings, retaining walls
- Average Price: $250 – $350 per cubic meter
- Pros: Greater strength, improved longevity, better resistance to cracking
- Cons: More expensive than basic concrete
Reinforced concrete is essential for high-stress areas such as multi-story buildings and heavy-duty industrial floors. If safety and longevity are priorities, investing in a stronger mix will save you money on repairs in the long run.
Specialty Concrete (Exposed Aggregate, Colored Concrete, Etc.): $300 – $450+ Per Cubic Meter
If you’re looking for decorative or customized finishes, specialty concrete is a popular choice. These mixes include exposed aggregate, polished, stamped, or colored concrete, allowing homeowners and builders to create visually appealing designs.
- Best For: Decorative driveways, pathways, patios, luxury homes
- Average Price: $300 – $450+ per cubic meter
- Pros: Aesthetic appeal, customizable, adds property value
- Cons: Higher cost, more complex installation process
The cost varies depending on the type of finish and customization options. For example, colored concrete requires specific dyes and pigments, while exposed aggregate needs specialized processing to reveal the decorative stones embedded in the mix.
DIY Vs. Ready-Mix Suppliers: Cost Comparison
When deciding between mixing concrete yourself or ordering from a ready-mix supplier, consider factors such as cost, convenience, labor, and project size.
- DIY Mixing is generally cheaper for small-scale projects but requires significant effort, precise measurements, and manual labor. It also comes with quality control risks, as variations in mixing can affect the durability and strength of the final product.
- Ready-Mix Concrete, on the other hand, provides consistent quality and precise mixing, making it the best option for larger projects like driveways, foundations, and commercial buildings. Although it has a higher initial cost, it saves time and reduces labor efforts, making it more efficient in the long run.
If you’re working on a small DIY project, purchasing individual bags of cement, sand, and aggregate might be a cost-effective solution. However, for larger-scale projects, ordering from a ready-mix supplier ensures you get a high-quality, well-mixed product that meets construction standards.
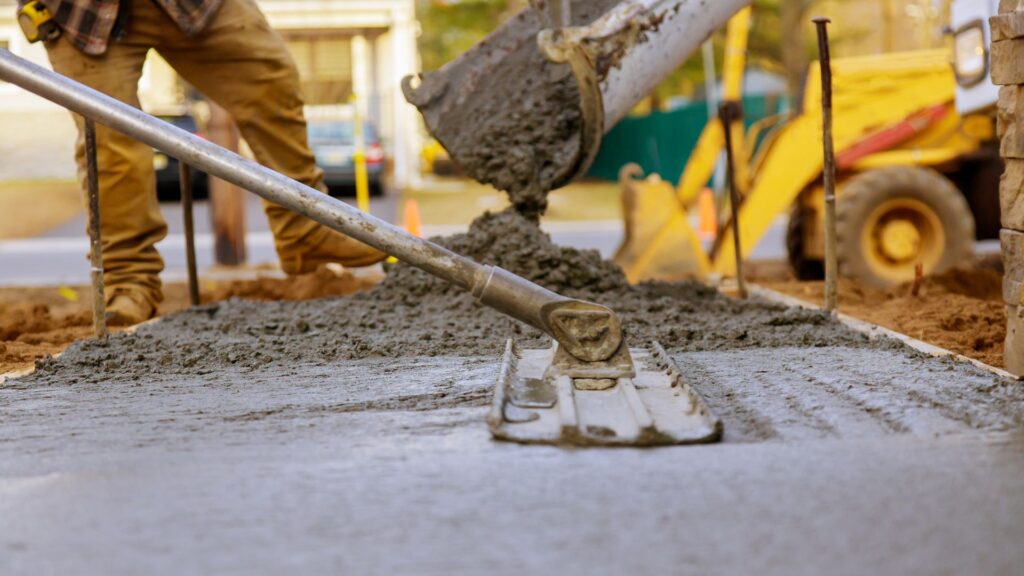
How To Get The Best Price For Concrete In NZ
Concrete is an essential part of many construction projects, but costs can quickly add up if you don’t plan ahead. Whether you’re building a driveway, laying a foundation, or working on a large-scale project, knowing how to get the best price per cubic meter can save you a significant amount of money. Below are some expert tips to help you secure the most competitive rates for concrete in New Zealand.
Compare Multiple Suppliers – Get Competitive Quotes
Not all concrete suppliers in NZ offer the same pricing, so it’s crucial to shop around before making a final decision. Prices can vary based on factors like location, quality of materials, and demand. Contact at least three to five suppliers in your area and request quotes. Be sure to ask about:
- Base Price Per Cubic Meter: Ensure the quote includes all material costs.
- Delivery Fees: Some suppliers offer free or discounted delivery within a specific radius.
- Additional Costs: Ask about potential extra charges for pumping, waiting time, or offloading.
- Bulk Discounts: If you’re ordering a large volume, suppliers may be willing to negotiate a better rate.
By comparing multiple quotes, you can identify the best balance between affordability and quality while avoiding overpriced options.
Order In Bulk – Save More On Large Projects
If you’re working on a big project, ordering concrete in bulk can lead to substantial savings. Many suppliers offer volume discounts, reducing the price per cubic meter when you purchase larger quantities. Bulk orders also ensure consistency in the concrete mix, which is critical for structural integrity.
When considering bulk orders, keep in mind:
- Storage & Timing: Ensure the project is ready for pouring before ordering large volumes.
- Batch Consistency: Using one supplier for the entire project prevents inconsistencies in mix quality.
- Discount Thresholds: Some suppliers offer discounts once you exceed a certain number of cubic meters.
If you’re working on a smaller project but still want to take advantage of bulk pricing, consider partnering with a neighbor, friend, or another contractor to place a joint order.
Plan Delivery Smartly – Reduce Transport Costs
Delivery costs can be a hidden expense when ordering concrete, especially if the supplier is far from your project site. Planning your delivery strategically can help you minimize these additional charges.
Ways To Reduce Delivery Costs:
- Choose A Supplier Nearby: The closer the supplier, the lower the transportation fees.
- Schedule Off-Peak Deliveries: Some companies charge more during peak hours due to high demand.
- Ensure Site Accessibility: If the delivery truck has trouble accessing your site, extra fees may apply.
- Combine Deliveries: If multiple concrete pours are needed, bundling them into fewer trips can save money.
By planning ahead, you can avoid last-minute fees and ensure a smooth and cost-effective concrete delivery process.
Consider Local Suppliers – Minimize Distance-Based Pricing
Opting for local suppliers is one of the best ways to cut costs, especially if you’re in a rural or remote area. Many major concrete suppliers charge higher delivery fees if they have to transport materials long distances. By working with a local concrete provider, you not only save on transportation costs but also support businesses within your community.
Benefits Of Choosing A Local Supplier:
- Lower Delivery Fees: Less distance means reduced fuel and labor costs.
- Faster Delivery Time: Concrete can reach your site sooner, minimizing project delays.
- Better Customer Service: Local companies are often more flexible and responsive to client needs.
If you’re unsure which local suppliers are available in your area, check online directories, read reviews, or ask for recommendations from contractors and builders.
Check For Seasonal Promotions & Discounts
Concrete prices fluctuate throughout the year due to supply and demand. During peak seasons (spring and summer), prices tend to rise because of higher construction activity. However, during off-peak months (autumn and winter), some suppliers offer discounts and promotions to attract customers.
How To Take Advantage Of Seasonal Discounts:
- Order Concrete During The Off-Season: Winter months often have lower demand, leading to better deals.
- Look For Special Promotions: Some suppliers run seasonal discounts or clearance sales.
- Ask About Loyalty Programs: Repeat customers or contractors working on multiple projects may qualify for reduced rates.
- Negotiate Early: Booking ahead of time can lock in lower prices before seasonal demand spikes.
By keeping an eye on seasonal trends and promotions, you can potentially save hundreds of dollars on your concrete order.
Final Thoughts: Get The Best Deal On Concrete In NZ
Concrete is a major investment, but with the right strategy, you can significantly cut costs without compromising on quality. Comparing suppliers, ordering in bulk, planning deliveries wisely, choosing local providers, and taking advantage of seasonal discounts are all effective ways to get the best price per cubic meter in New Zealand.
Before making a purchase, always do your research, ask the right questions, and negotiate where possible. Whether you’re working on a small DIY project or a large construction job, these cost-saving tips will help ensure you get top-quality concrete at the best possible price.
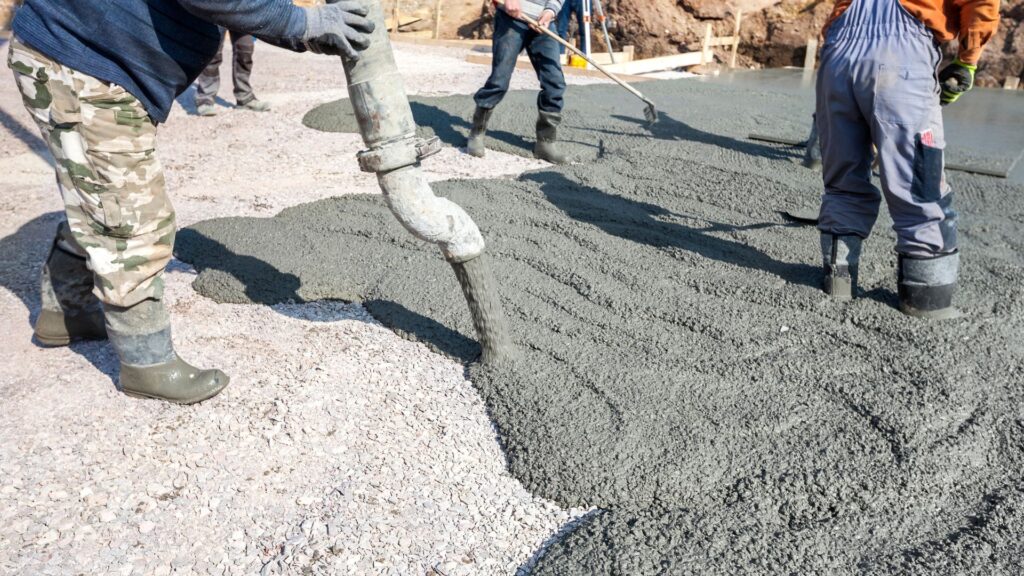
DIY Vs. Hiring A Professional: Cost Considerations
When planning a concrete project, one of the biggest decisions you’ll face is whether to do it yourself (DIY) or hire a professional contractor. While DIY might seem like a cost-saving option, there are several important factors to consider, including material costs, labor, efficiency, and potential risks. Below, we’ll break down the costs of both approaches and weigh the pros and cons so you can make the best decision for your project.
Cost Of Doing It Yourself: Materials, Tools, And Potential Waste
Taking the DIY route can seem appealing, especially for small-scale projects like patios, garden paths, or shed foundations. However, there are several cost factors to keep in mind:
- Materials Can Be Expensive In Small Quantities – Buying cement, sand, and aggregate separately may seem cheaper than ordering ready-mix concrete, but small-scale purchases often cost more per unit. Additionally, miscalculating the amount needed could lead to unnecessary expenses or shortages, forcing you to buy more at a premium.
- Specialized Tools May Need To Be Purchased Or Rented – Concrete work requires equipment like mixers, trowels, screeds, and wheelbarrows. Renting these tools adds to the overall cost, and if you buy them, they may not be used frequently enough to justify the investment.
- DIY Concrete Work Is Labor-Intensive And Time-Sensitive – Concrete must be mixed, poured, leveled, and finished within a set timeframe. If mistakes are made, such as improper leveling or delayed finishing, the concrete may set incorrectly, leading to cracks and durability issues.
- Potential Waste Can Drive Up Costs – Mixing errors, spillage, or using the wrong concrete strength could result in wasted material and additional expenses to fix mistakes. A poorly executed DIY project might even require complete removal and replacement, doubling costs.
Cost Of Hiring A Contractor: Labor, Efficiency, And Quality Assurance
While hiring a professional contractor has a higher upfront cost, it also comes with significant benefits in terms of expertise, efficiency, and quality. Here are key cost considerations when choosing a professional:
- Labor Costs Reflect Skill And Experience – Contractors charge for their expertise, which includes precise site preparation, concrete pouring, finishing, and cleanup. Although this adds to the expense, it ensures high-quality results that last longer.
- Professionals Can Source Materials At Competitive Prices – Many contractors have relationships with suppliers, allowing them to buy concrete at lower rates than what’s available to the general public. This can help offset some labor costs.
- Specialized Equipment Is Included In The Service – Hiring a contractor means you won’t need to rent or purchase tools like concrete mixers, laser levels, or power trowels, saving you money and hassle.
- Quality Work Reduces Future Repair Costs – Properly installed concrete is more durable, reducing the chances of cracking or deterioration. Contractors also follow best practices to ensure your project meets industry standards, avoiding costly future repairs.
- Compliance With Building Regulations Is Guaranteed – Some concrete projects, such as driveways or foundations, may require adherence to local building codes. A contractor ensures compliance, preventing potential fines or issues with inspections.
Pros And Cons Of DIY Vs. Hiring A Professional
Both DIY and hiring a contractor have distinct advantages and disadvantages depending on your budget, experience level, and project complexity.
- DIY Is More Affordable But Riskier – If you have prior experience and only need a small amount of concrete, handling the job yourself could save money. However, for beginners, the risks of mistakes, material waste, and rework could make DIY more expensive in the long run.
- Hiring A Professional Is A Higher Upfront Cost But Offers Peace Of Mind – If your project requires structural integrity, such as a driveway, patio, or foundation, professional installation ensures long-term durability and compliance with industry standards.
- DIY Works Best For Small, Non-Structural Projects – Simple pathways, small garden slabs, or decorative concrete features are ideal for DIY. Larger jobs requiring precision, heavy loads, or structural integrity are best left to professionals.
Final Thoughts: Which Option Is Right For You?
If you’re confident in your skills and working on a small, non-structural concrete project, DIY may be a cost-effective solution. However, for larger projects that require durability, strength, and long-term reliability, hiring a professional is often the better investment.
Before deciding, consider getting a professional quote and comparing it with your DIY cost estimate. This way, you can determine which option provides the best balance of cost, quality, and efficiency for your project.
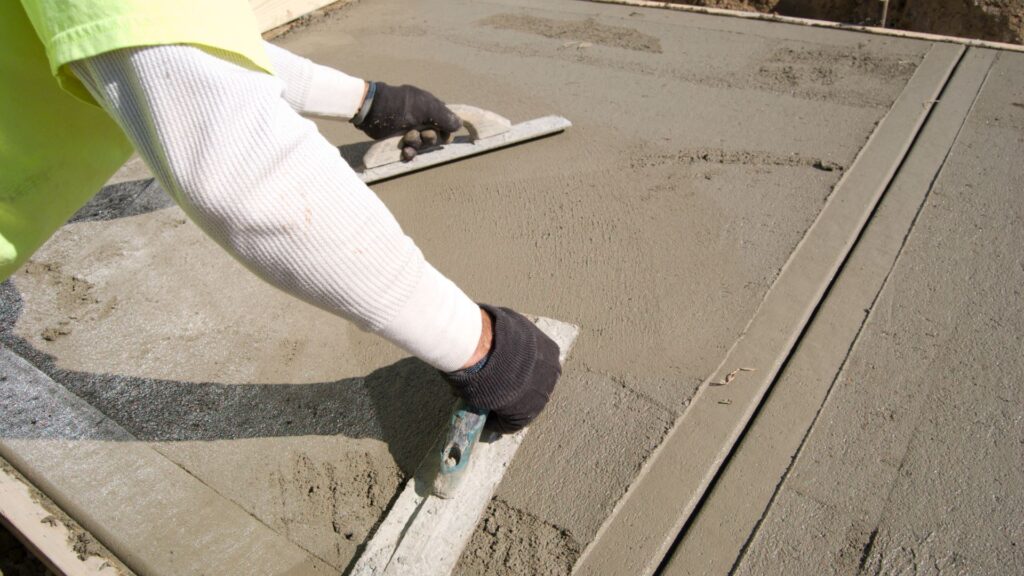
Common Mistakes That Can Increase Concrete Costs
When it comes to concrete projects, budgeting accurately is just as important as selecting the right materials. Many homeowners and contractors unknowingly make costly mistakes that drive up expenses. To help you avoid unnecessary spending, let’s break down some of the most common errors that can increase the price of concrete and how to prevent them.
Underestimating Material Needs: Leads To Additional Small Orders At A Higher Cost
One of the biggest mistakes in concrete planning is failing to calculate the exact amount needed for a project. Ordering too little concrete often results in having to place a second order, which can be far more expensive than getting it right the first time.
Concrete suppliers typically charge a minimum load fee, meaning smaller orders cost disproportionately more per cubic meter. Additionally, last-minute orders can cause project delays and may include urgent delivery surcharges.
How To Avoid This Mistake:
- Use a concrete volume calculator to estimate your required cubic meters accurately.
- Add 5-10% extra to account for spillage and unforeseen issues.
- Consult with your supplier or contractor to double-check your calculations.
Ignoring Site Preparation: Poor Ground Conditions May Require Extra Work
Proper site preparation is crucial for ensuring a smooth and cost-effective concrete pour. If the ground is uneven, unstable, or has drainage issues, it can lead to excessive material usage, delays, and even structural problems in the future.
For example, if the soil is too soft, additional gravel or compacting may be needed before pouring, adding extra costs to your project. Similarly, failing to clear debris or properly form the area can cause wasted concrete, increasing expenses.
How To Avoid This Mistake:
- Clear the site of rocks, roots, and debris before the concrete truck arrives.
- Ensure the ground is compacted and leveled to prevent uneven concrete thickness.
- Plan for proper drainage and formwork, so the concrete doesn’t shift or settle incorrectly.
Last-Minute Changes To Mix Or Quantity: Can Increase Costs Significantly
Changing your concrete mix type or quantity at the last minute can be one of the most expensive mistakes. Suppliers may charge extra for adjustments after the initial order, and sudden changes can lead to delays that impact labor costs.
For instance, if you decide to upgrade to a higher-strength mix (like 30MPA instead of 20MPA) on the day of the pour, this could lead to higher material costs and extra processing time. Similarly, ordering too much or too little concrete due to last-minute adjustments can disrupt workflow and inflate costs.
How To Avoid This Mistake:
- Finalize your concrete mix and volume well in advance.
- Confirm your order with the supplier at least 24-48 hours before delivery.
- Work with a professional contractor to ensure the mix meets your project’s requirements from the start.
Choosing The Wrong Concrete Mix For The Project: May Lead To Future Repairs
Selecting the wrong concrete mix can result in long-term durability issues, leading to costly repairs or even full replacements down the road. Different projects require different strengths and compositions, and using an inappropriate mix can cause cracks, premature wear, or insufficient load-bearing capacity.
For example, a low-MPA concrete mix might be fine for a footpath but would fail under the weight of a driveway or parking area. Similarly, failing to use reinforced concrete where necessary could lead to structural failures, forcing you to redo the work.
How To Avoid This Mistake:
- Understand the MPA (megapascal) rating required for your project.
- Consult with a concrete specialist or supplier to determine the best mix for your needs.
- If your project is exposed to harsh weather or heavy loads, consider reinforced or waterproofed concrete to prevent premature wear and cracking.
Avoiding these common mistakes can save you hundreds—if not thousands—of dollars on your concrete project. By carefully planning your material needs, preparing the site, sticking to your original order, and choosing the right mix, you can keep costs under control while ensuring long-lasting quality.
If you’re planning a project and want the best concrete prices in New Zealand, be sure to compare quotes from reputable suppliers and consult an expert to avoid costly errors.Ready to start your concrete project? Get the best prices on high-quality concrete in New Zealand! Whether you’re working on a small DIY job or a large-scale build, we provide reliable, cost-effective solutions. Get a free quote today!
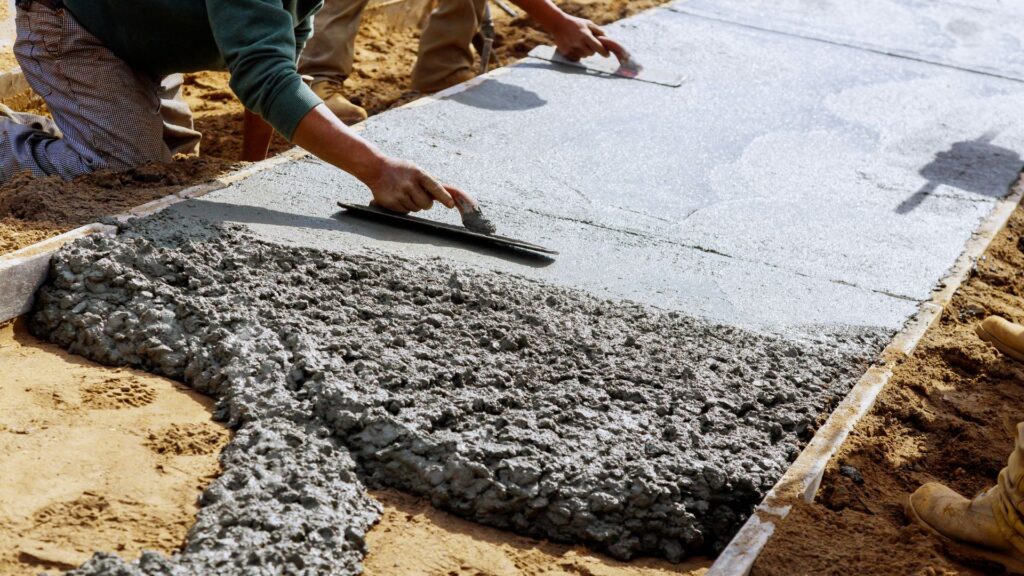
FAQs: About Concrete Price Per Cubic Meter In NZ
The average price of concrete in New Zealand ranges from $180 to $250 per cubic meter, depending on factors like location, supplier, mix type, and additional costs like delivery and pumping fees. Specialty concretes, such as decorative or high-strength mixes, tend to be more expensive.
Several factors affect the price of concrete, including the type of mix, strength rating (MPA), supplier location, transportation costs, seasonal demand, and additional additives such as waterproofing agents or reinforcements. Bulk orders and proximity to suppliers can also impact pricing.
Mixing concrete yourself can be cheaper for very small projects, but for larger jobs, ready-mix concrete is often more cost-effective and ensures consistency and quality. Buying individual cement, sand, and aggregate components can be time-consuming and may lead to errors in mixing, which can affect durability.
o calculate the amount of concrete needed, use the formula: Length (m) × Width (m) × Depth (m) = Volume in cubic meters (m³). It’s always a good idea to order a little extra (typically 5-10%) to account for spillage and variations in site conditions.
Yes, additional costs may include delivery fees, long-distance transport charges, concrete pumping services, and waiting time fees if the site is not ready for pouring. It’s best to check with your supplier for detailed pricing on these extras.
MPA (megapascals) measures the strength of concrete. 20MPA concrete is suitable for basic residential projects like footpaths and driveways, while 30MPA or higher is used for structural applications, commercial buildings, and heavy-load areas. Higher-strength concrete costs more due to the increased cement content and additional processing requirements.
Yes, concrete prices can fluctuate due to seasonal demand, material costs, and fuel prices for transportation. During peak construction seasons (spring and summer), prices may be slightly higher due to increased demand. Booking in advance can sometimes help secure a better rate.
Yes, especially for large orders. Many suppliers offer bulk discounts, and comparing quotes from multiple providers can help you get the best deal. Some suppliers may also provide price breaks for repeat customers or long-term contracts.
To reduce costs, consider ordering in bulk, choosing a supplier close to your site, preparing the site in advance to avoid delays, and opting for standard mixes instead of specialty concretes unless necessary. Checking for seasonal promotions or discounts from suppliers can also help.
You can find trusted concrete suppliers by searching online directories, checking customer reviews, or asking for recommendations from local builders and contractors. Many suppliers also provide online price estimates or free quotes to help you compare costs.
Conclusion
Understanding Concrete Price Per Cubic Meter In NZ is essential for anyone planning a construction project, whether it’s a simple home DIY task or a large-scale commercial build. Prices can vary due to factors such as concrete type, supplier location, delivery fees, and additional costs like pumping services or special additives. To ensure you get the best value, it’s always wise to compare multiple quotes from different suppliers, as pricing can fluctuate based on demand and location. Doing thorough research, planning ahead, and considering bulk orders can help reduce overall costs while ensuring high-quality results. If you’re ready to take the next step, explore reputable concrete suppliers in your area to find the best pricing and service options.
About the Author:
Mike Veail is a recognized digital marketing expert with over 6 years of experience in helping tradespeople and small businesses thrive online. A former quantity surveyor, Mike combines deep industry knowledge with hands-on expertise in SEO and Google Ads. His marketing strategies are tailored to the specific needs of the trades sector, helping businesses increase visibility and generate more leads through proven, ethical methods.
Mike has successfully partnered with numerous companies, establishing a track record of delivering measurable results. His work has been featured across various platforms that showcase his expertise in lead generation and online marketing for the trades sector.
Learn more about Mike's experience and services at https://theleadguy.online or follow him on social media: